PROJECTS
Grocery Portal
Designed, built, and programmed a self-serve curbside pickup prototype
Created a simulator to see how a fleet would work in a parking lot
Trained a binary classifier for tote empty detection using synthetic data generated with Blender
Programmed in Python and C++
Pipedream Labs
Wait 3-5 seconds for images to load
Trailer Unloader End of Arm Tool
Custom suction cup manifold for zone control
Custom conjugate cam to control the 2-axis motion with a single servo
Pneumatic guide-rails with a proportional valve for variable control
Complex conveyor routing (15 bends hidden)
Sensing a/ Electronics includes 2 lidars, 3 servos, and laser rangefinders
Bastian Solutions R&D
Cam-based Gearbox
Instead of using rotating gears, I had geared "feet" that walked along an inner gear, actuated by a rotating cam. With this method, I could achieve ratios of 100:1 in a single stage with zero backlash.It was very loud and not very practical, but it was a fun exercise that gave me a really good understanding of cams.
Motus Labs
Telepresence Robot
Created a telepresence robot that communicates through webRTC and ROS2
Can be controlled by anyone with just a link, achieved 120 ms control latency between Austin and DC
Designed custom capstan drive for tablet gimbal
Personal Project
Wait 3-5 seconds for images to load
AMR Dynamometer
Used for testing missions on AMR
Designed and built up machine and control cabinet
Controlled resisting torque through servos via Ethercat
Programmed with Python/C++
Pipedream Labs
Construction plotter
Construction workers use chalk lines to plot the layout of their building. With a buddy, designed and programmed a collab robot to automate this process.
Personal Project
Autonomous Mobile Base (WIP)
Designed and built an AGV base for testing outdoor localization with a 3D camera
4 m/s max speed w/ a 200 lb payload
ROS2 stack
Personal Project
Zero-backlash High Ratio Gearbox
Led a team of 3 total engineers and 1 contractor
Created the base design that the rest of the product line would base off of
Wrote scripts to create custom geometry and parse test data
FEA and Motion simulation
Motus Labs
Gearbox Testbeds
Positional accuracy
Load testing misalignment coupling dispacks
Heavy load and life testing
Motus Labs
Fascia and end-effector design
Designs debuted at CES!
3D printed with Markforge
Haddington Dynamics
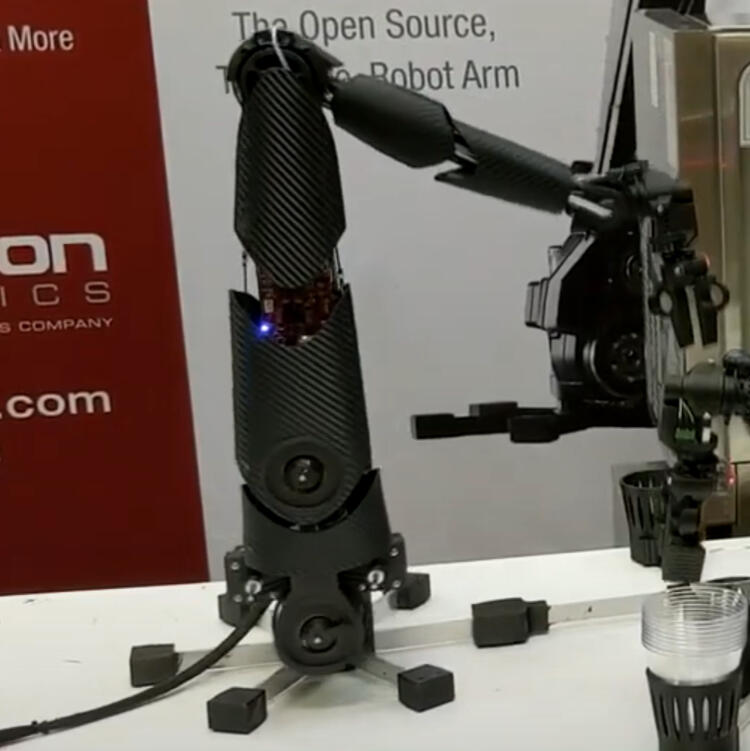